Key Takeaways
- What is CNC: CNC stands for computer numerical control, which is a process of using computer software to control the movement and operation of machines that can cut, carve, or engrave materials.
- Types of CNC machines: There are different types of CNC machines, such as routers, mills, lathes, lasers, and plasma cutters. Each machine has its own advantages and disadvantages depending on the material, shape, and complexity of the workpiece.
- Benefits of CNC machining: CNC machining offers many benefits, such as high precision, accuracy, speed, efficiency, and flexibility. CNC machining can produce complex and customized parts that are difficult or impossible to make by hand or with conventional tools.
- How to start a CNC business: Starting a CNC business requires careful planning, research, and investment. You need to identify your target market, your products or services, your equipment and tools, your marketing and sales strategies, and your financial projections. You also need to consider hiring staff, expanding workspace, and seeking funding as you grow.
CNC, or Computer Numerical Control, encompasses the manufacturing process where machines cut, carve and form parts based on computer codes that control the cutting tool’s speed and movement.
These machines cut metals, wood, foam, composites, plastics and more into precise parts with uses in almost every industry.
They do this autonomously and without any human intervention once the manufacturing code is generated, greatly improving manufacturing speed, efficiency, repeatability, reliability, and precision – and they can potentially go 24/7.
Top CNC brands offer a variety of different CNC machining types, from CNC milling machines to lower-cost CNC routers, as well as lathes, grinders, laser cutters, EDM machines, and water jet cutters. The CNC industry market size is worth billions, and continues to grow.
3D printers are technically also types of CNC machine, though they use additive manufacturing rather than subtractive manufacturing techniques.
In this guide, I’ll walk you through all the key points I’ve learned about CNC over the past 10 years, so you have a solid foundational knowledge to start producing successful projects.
- Key Takeaways
- A quick introduction to CNC
- History of CNC
- The CNC Process
- G-code and M-Code Files in CNC
- Types of CNC machines
- 3-Axis CNC machines vs 5-Axis CNC Machines
- Open loop vs closed loop CNC machining systems
- Problems with CNC and possible errors
- CNC vs 3D printing: Additive vs subtractive manufacturing
- NC vs CNC
A quick introduction to CNC
CNC movements are based on the X, Y and Z axes. The tool is positioned using stepper or servo motors, which act on the movements based on the code obtained from the original 3D model of the part you want to create – called the G-code.
Numerical controls describe how fast to move the spindle (the rotating part which spins the tool holder), which direction to move, which tool to use (if the machine uses multiple tools and can switch between them), as well as other factors such as using coolant.
CNC operators run and monitor machines, and CNC programmers create and run the codes for them.
History of CNC
Before CNC existed, there was only NC. This means Numerical Control (without the “C” of Computer), where back in the 1950s punched tape was used to manually input commands on to data cards to describe where to move the machine and tools to cut parts. This was far slower, less efficient, and more prone to human error.
Then along came the first computers. These early computers, though primitive, could produce their own punched tape based on certain inputs. This dramatically increased the speed at which commands could be produced. As computers advanced, Computer Numerical Control – CNC as we know it – grew in efficiency, speed and in the visualization and previewing of parts possible with 3D software modeling tools.
Now in the modern day CNC machines are fully automated. Simply give them the part code in the form of a digital file – usually a G-code file – and the machine will take care of the rest. Based on these custom instructions within the G-code file, the machine can be programmed for exact speeds, positions, and can switch out tools for different parts of the process to get the best results.
Some machines use huge tool libraries and store dozens of tools for use in different niche applications.
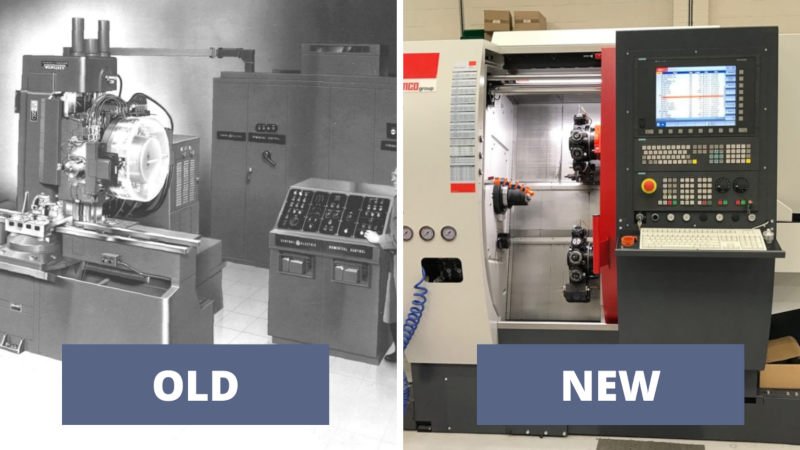
The CNC Process
- Step 1: First, the CNC machining process starts with a CAD model, a 3D model designed on a CAD software for the desired shape and size to be created. You may either want to design the part yourself if you have the skills, or have a designer create the model.
- Step 2: The CAD model is then imported into a CAM software which prepares the model for the actual machining process.
- Step 3: You will then need to choose the parameters for the CNC process, such as the cutting speed of the tool. Different velocities and other factors work best in different situations and for different materials and machines. Professional CAD-CAM software can also optimize part layout to use the least material possible. The CAM software checks for any errors, and exports the part as a G-code file which tells the machine the speed, coordinates, and a variety of other important factors.
- Step 4: After this, the operator trials the G-code or other program to check for any clear mistakes, before running the machining operation.
G-code and M-Code Files in CNC
Within CNC there are two main file formats that affect the CNC machining process. Most people have heard of G-code, which are used in both CNC and 3D printing, but M-codes are also important.
G-code files: stands for geometry code, and includes the machine’s movement coordinates so that the machine knows where to cut chips off the part, which type of CNC machining tool to use, how quickly to move the spindle, the radius of arcs given by the machine, and also the speed settings.
M-code files: all the major factors not covered by the G-code are covered in the M-code. M-code describes miscellaneous code and comes with the overall G-code, but accounts for different parts of the CNC process. The M-code accounts for when to stop axes or the spindle, when to change direction of spinning e.g. from clockwise to anticlockwise, and when to use coolant.
The best combined CAD-CAM software packages can both design and prepare your 3D CAD model for production to produce G-code files.
Get a grasp on CNC technical terms and acronyms, read our CNC Terminology Guide.
Types of CNC machines
CNC Milling
Perhaps the most common form of CNC machine, CNC mills use a rotating cutting tool to remove chips from a block of material. CNC milling tools include end and chamfer mills, and face milling cutters.
CNC mills have a cutting tool in a spindle, which rotates the tool to make the cuts. The spindle spins the tool to high speeds, then the workpiece is moved to cut unnecessary parts off. Both 3-axis mills and 5-axis mills exist, with 5-axis mills capable of more intricate cutting.
CNC milling is a very accurate and versatile process suitable for a variety of applications, is able to shape metals, plastics and wood, and is also very quick.
However, as a subtractive manufacturing process lots of waste is generated, and many different tools are required for more complex projects. These factors make CNC milling an expensive and industrial process.
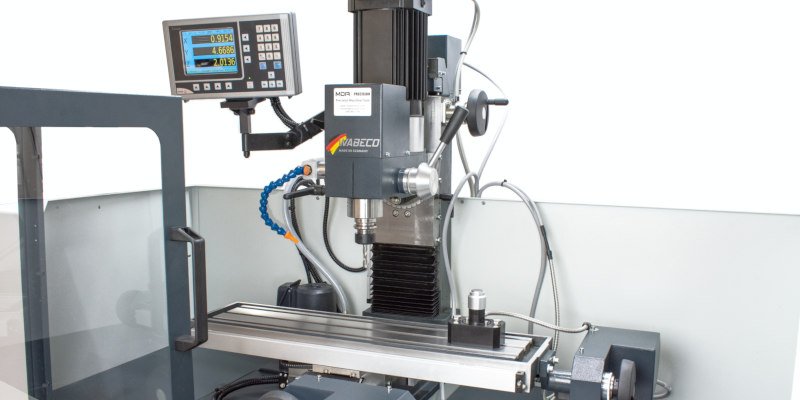
CNC Lathes and Turning
CNC lathes rotate spin the workpiece in the spindle (rather than the mill tool head in mills), with a fixed cutting tool slicing chips from the spinning part.
The process, called turning, is ideal for symmetrical parts, and though it is more limited in terms of the number of axes, lathes are precise and accurate, and commonly used to produce shafts and gears.
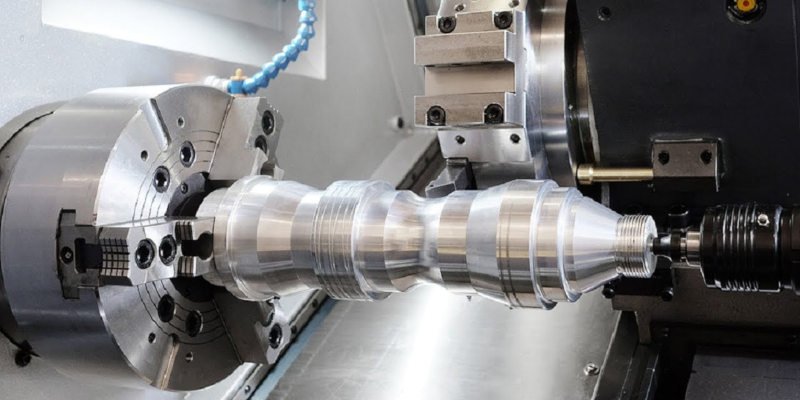
CNC Routers
CNC routers are similar in form to CNC milling machines – they both feature a rotating cutting head. Routers however are better for softer materials, especially wood, as they are typically less powerful and accurate, and a more for hobbyists and less industrial uses.
DIY CNC router kits can be purchased for homemade CNC router projects, which are great for accurate woodworking projects.
We also published a full guide explaining how deep a CNC router can cut .
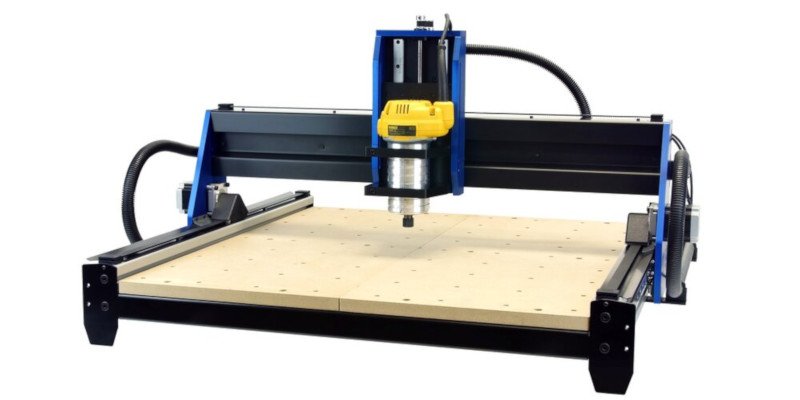
Water Jet Cutters
Water jet cutters can cut granite, metals, and other tough materials. They use high-pressured water, sometimes mixed with abrasive substances like sand, to machine factory parts and other applications.
As less heat is used during the water jet cutting process than most other CNC types, it is commonly used to cut materials that would otherwise have their properties changed by heat. The process is also very precise, and is useful for very intricate carving and cutting.
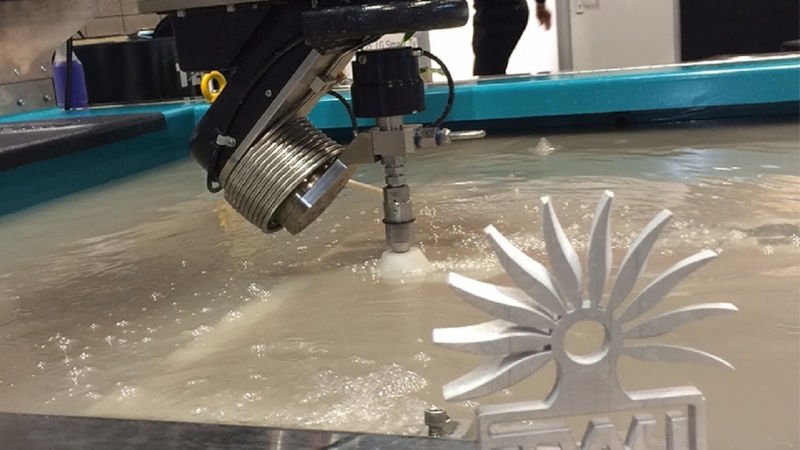
Electrical Discharge Machines (EDM machines)
Sometimes called die sinking or spark machining as well as spark eroding, EDM machining involves electrical discharges from sparks to cut and shape parts.
EDM machines use current discharges and an electric field to remove chips from the workpiece. Two electrodes are used, with electrical fields intensified by moving the electrodes nearer to each other in order to cut pieces. A dielectric liquid separates the two electrodes and facilitates the voltage.
There are three main types of EDM machines:
- Wire EDM machines: use a wire as the electrode to cut materials such as hardened steel (or other conductive materials).
- Sinker EDM machines: use dielectric liquids with the electrode and work piece to cut the workpiece.
- Fast hole drilling EDM
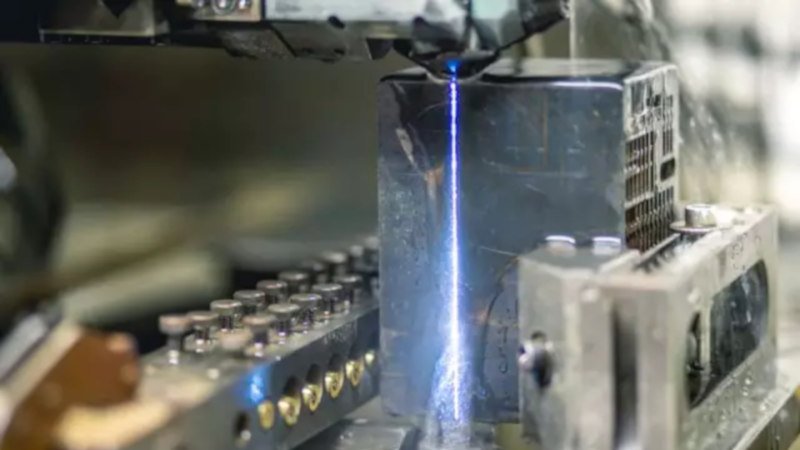
CNC Drilling
Similar in form to CNC mills, CNC drills use a spindle and drill but rather than forming a part, instead only cut holes. These holes can be precisely designed for size, diameter, and depth.
Other common forms of CNC machine include:
- Laser Cutters
- Plasma Cutters
- Flame Cutters
- Press brakers
- Embroidery machines
- Multi-spindle machines
- Turret punchers
- Wire-bending machines
- Foam cutters
- Cylindrical grinders
- Glass cutters
- Grinders & Abrasive Cutters
3-Axis CNC machines vs 5-Axis CNC Machines
3-axis CNC machines were the original standard for machining, able to move and cut across three axes: X, Y, and Z. However, there are some limitations with machining deep parts, especially those with deep and difficult cavities.
5-axis CNC machines build on this, adding A and B axes to the original X, Y and Z axes. A and B are axes around which the tool, such as the CNC milling tool, can rotate. The tool can rotate around the X and Y axes – moving the table, increasing geometric versatility. This improves machining speed, precision and only requires shorter tools, though does increase preparation time (but reduces material handling time).
For complex, tall, deep, or intricate parts, 5-axis CNC machines work best.
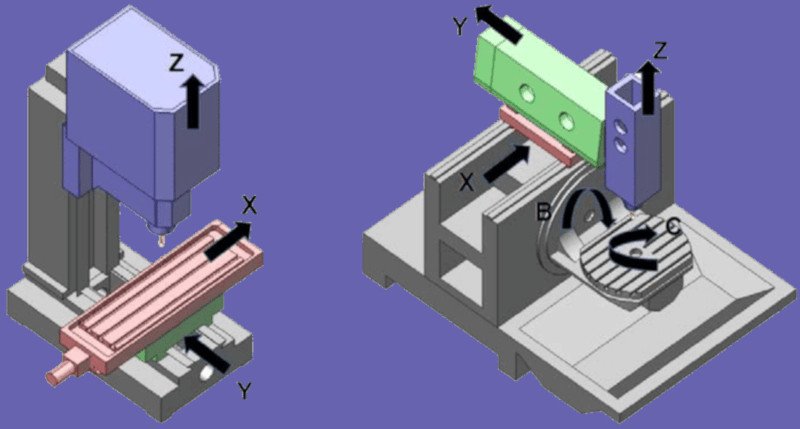
Open loop vs closed loop CNC machining systems
Open loop stepper systems run in one direction – from the controller to the stepper motor. On the other hand, closed loop systems run two ways, and can therefore receive feedback. If, for example, a CNC router misses a step, a closed loop system can attempt to correct the error, or stop and prevent crashing.
Without feedback, if errors occur there is no way for an open loop system to know. It will therefore carry on until either you stop the machine, or a limit switch is hit.
Open loop systems are cheaper, and therefore more common on DIY CNC routers, but closed loop systems are more advanced and can correct errors, such as in position of the machine.
Problems with CNC and possible errors
Though efficient, precise and generally reliable, CNC can go wrong. Errors can occur, and sometimes they can badly damage not just the material, but the CNC tool and machine. The piece or the machine can be incorrectly placed, causing a crash where the tools break. Incorrect code or other factors can contribute.
Linear, rotary and angle encoders can be used with servo motors and other systems to minimize errors by checking the machine is moving as expected. Moreover, industrial closed loop machines significantly reduce errors as the control always knows the axis position.
CNC vs 3D printing: Additive vs subtractive manufacturing
Unlike 3D printing, CNC is subtractive rather than additive. The CNC process starts with a larger block of material as the workpiece, and removes areas, like chipping away at marble – to get to the final model.
3D printers instead use additive manufacturing technologies. They take 3D model data and import it into a 3D slicer, which slices the part into layers for the 3D printer to deposit material or selectively solidify resin or powder to create the finished part.
3D printers waste less material as they only deposit the material necessary to create the part, but CNC machining is faster and can handle tougher materials more easily. 3D printing is considered best for very short run, intricate parts with complex geometries, with CNC better for faster, cheaper parts in metal, wood or other tough materials.
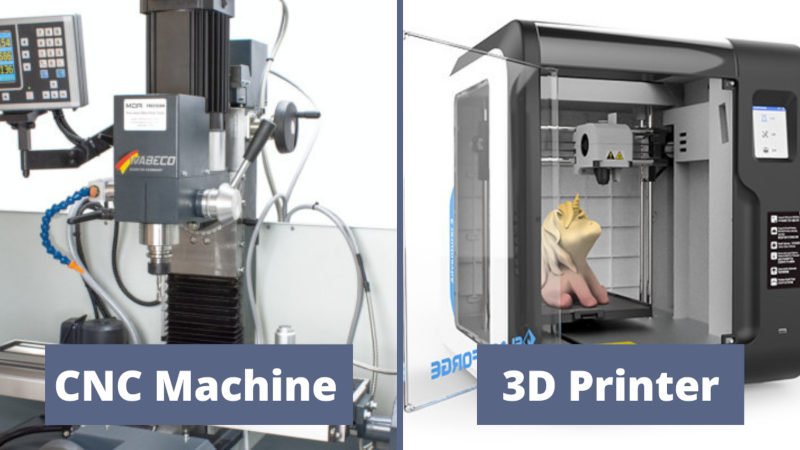
NC vs CNC
Numerical Control machines are controlled by numerical instructions called programs. These are fed into the machine via punch cards, requiring skilled operators to monitor and use. NC machine programs are difficult to modify, for example if errors occur.
Computer Numerical Control machines instead use computer programs, written in alphanumeric data, with detailed coded instructions for movement and manufacturing method. CNC code can be far more easily edited and improved if errors occur, and CNC is considered significantly more efficient and effective.
Related articles:
- How much does a CNC cost? A complete CNC machine price guide
- What is an NC vs CNC machine? The differences explained
- Workshop must-haves: essential CNC router accessories