Key Takeaways
- Depth of cut: The depth of cut is the height of the material that is removed by the CNC router in one pass. It depends on various factors, such as the tool geometry, the material, the feed rate, and the spindle power.
- Z-axis limit: The Z-axis of the CNC router determines how deep it can cut in total. It is the distance between the spindle and the workpiece. CNC routers have a shorter Z-axis than CNC mills, which limits their cutting depth.
- Flute length: The flute length of the router bit is the length of the cutting edges on the sides of the bit. It limits the maximum depth of cut for each pass. The flute length should not exceed the depth of cut, or it will cause inefficiency and damage.
- Vibrations: Vibrations are a major problem when cutting with helical tools, which have spiral flutes. They can damage the spindle, the tool, and the workpiece. To avoid vibrations, the depth of cut should be an integer multiple of a certain length, which depends on the tool diameter, number of teeth, and helix angle.
Generally, CNC routers can cut up to about an inch in one pass, and different CNC machines can cut maximum depths of between 1-7 inches.
Though, how deep a CNC router cuts depends on many factors, including the Z-axis, the flute length, vibrations, tool diameter, material, spindle power, feed rate (or chip load), and radial depth of cut.
I’ll explain them all in more depth in this article.
If you don’t know how deep to plunge the CNC tool, you risk breaking the bit, causing vibrations, reducing tool life, increasing production times, and a lot more that I’ll discuss.
In my career I’ve dealt with this countless times, and so I’ve taken into account various mathematical formulas, various CNC router forces, and cutting scenarios. So, here’s a technical explanation of how deep a CNC router can cut.
Stepdown vs Stepover (Axial Depth of Cut vs Radial Depth of Cut)
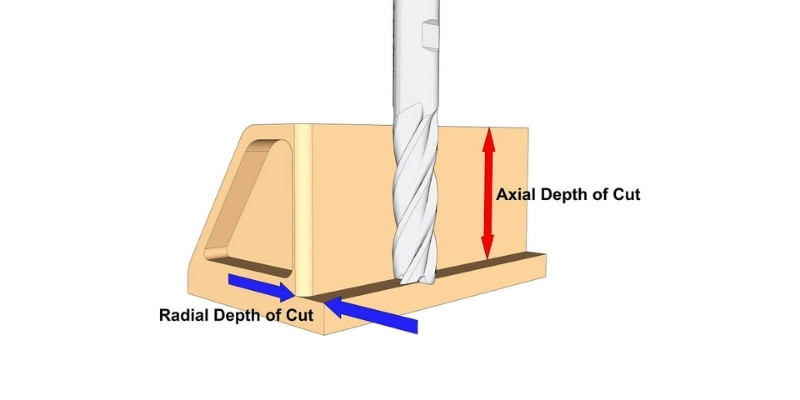
When I talk about the depth of cut, I mean the axial depth of cut, or the stepdown. It’s the height of the material that gets removed (in every pass), or the height of the CNC tool that engages the material.
There is also the radial depth of cut, which we also call the stepover, or the width of cut. It’s the width of the material that’s removed in every pass. In other words, it’s the portion of the tool’s diameter that’s engaging the material.
I’ve also written a more detailed article covering stepover and appropriate stepover values in various CNC operations.
Factors That Limit the Depth of Cut in CNC Routers
The Z-Axis
CNC routers have a short Z-axis, and they can’t cut deeper than their Z-axis allows. This is the first limit we encounter: a CNC router can cut as deep as its Z-clearance as a best-case scenario (the best scenario being that the Z-axis is also large enough to accommodate the tool length).
In comparison, CNC mills have a C-column that allows for a large Z-axis that can cut much deeper than routers.
We’re not talking about the depth of cut here, but how deep the machine can cut.
If you’re wondering what’s the deepest a CNC router can cut in multiple passes, look at its Z-clearance minus some inches of room for the cutting tool. Also, consider how much the Z-axis can travel down when the tool rests on the stock.
So, CNC routers can cut about 0.5-7 inches deep, depending on how large the machine’s Z-axis is.
For a more detailed answer explaining the differences in how deep CNC mills can cut versus routers, you can also read my article on CNC mills versus CNC routers.
Flute Length
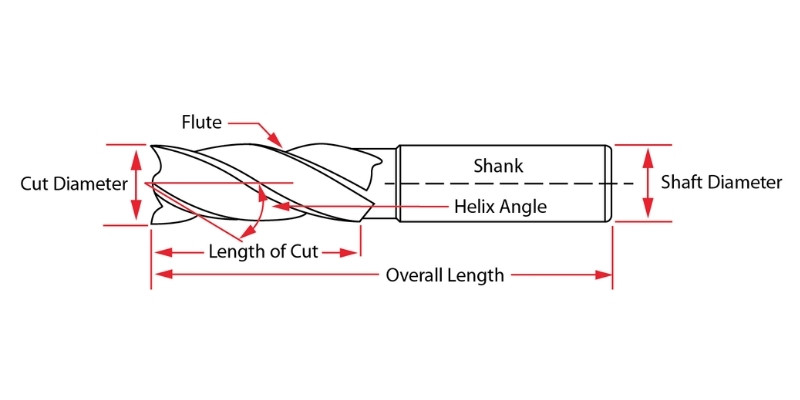
The CNC router bit’s flute length limits the maximum cutting depth.
CNC routers use router bits that typically have flutes on the sides, such as straight or spiral flutes. These flutes help remove the material as the bit rotates.
The depth of cut (or stepdown) is determined by the length of the flutes on the router bit. If a router bit has 1-inch flutes, it means that the maximum depth of cut or stepdown should not exceed 1 inch.
If you did, you’d cut less efficiently, increase the wear on the bit, and potentially even damage your CNC router.
So far, we’ve determined the deepest cut limit (from the Z-axis) and the maximum stepdown from the flute length. But, what’s the correct depth of cut in a CNC router?
Technical Constraints on Depth of Cut in CNC Routers
Vibration in Helical Tools
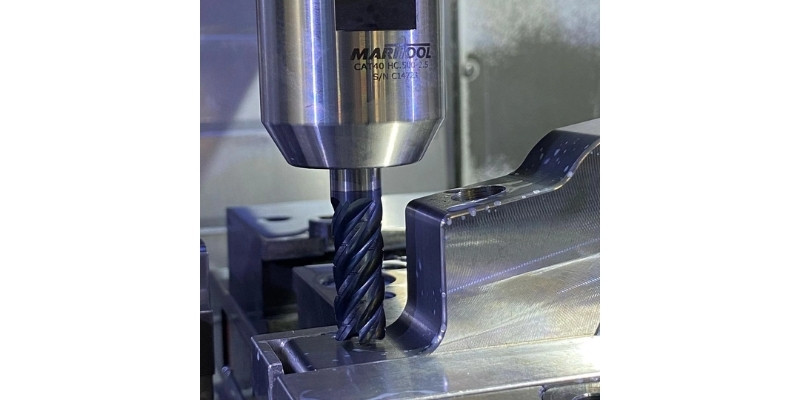
Router bits with straight edges are less prone to vibrations than endmills with helical flutes, so, if you’re cutting wood with straight router bits, you’re in luck.
However, endmills that have helical flutes can cause problematic vibrations when cutting. This is the most important factor when deciding your depth of cut: you can’t plunge a helical tool with random step downs or you’ll get terrible vibrations that will ruin your spindle’s bearings, the tool, and probably your whole CNC router.
To avoid unwanted vibrations, it’s best if the depth of cut is integer multiple of a certain length (we call them harmonics). But, the depth of cut is still limited by other factors that we’ll explain shortly, like the tool geometry, the chip load, the material, and the machine rigidity. These factors are even more vital and have a higher priority.
So, for example, if the shortest correct depth of cut for a certain helical tool is 0.5mm, you should only use 0.5mm increments (0.5mm, 1mm, 1.5mm, etc, but not 1.25mm).
The formula is:
axial depth of cut = nπD / (z * tan(𝛌))
Where:
- n can be any positive integer representing the various multiples (harmonics)
- D is the tool diameter
- z is the number of flutes
- and 𝛌 is the angle of the helix with respect to the tool’s centerline.
For example, let’s consider a tool with a diameter of 6mm (D = 6mm), four teeth (z = 4), and helix angle of 1 (𝛌 = 1).
Using the formula, the acceptable step downs would be calculated as follows: n * 3.14 * 6 / (4 * 1) = 4.71n.
Therefore, you can safely plunge this tool using step downs such as 4.71mm, 9.42mm, 14.13mm, and so on.
Tool Diameter
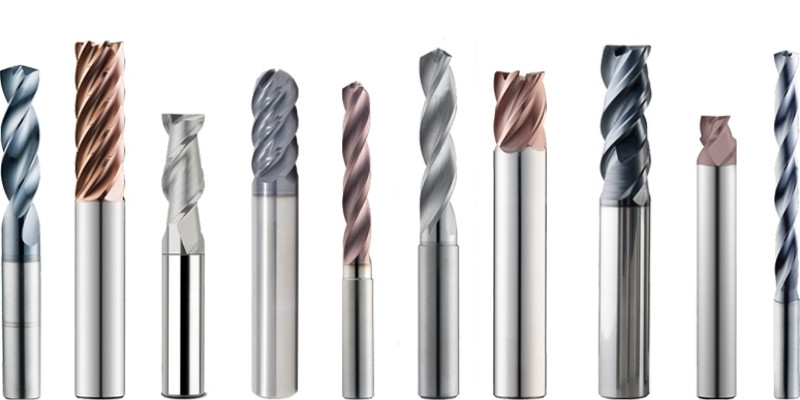
Tools with larger diameters can cut deeper than smaller diameters. This is because when cutting too deep with a high feed rate, there is a risk of tool deflection, which can lead to tool breakage. To avoid tool deflection, it is generally better to reduce the depth of cut rather than lowering the feed rate.
Carbide tools are often capable of cutting 4-10 times their own diameter, provided that the feed rates are adjusted accordingly.
However, this cutting ratio tends to be higher for smaller bits. For example, a ¼” bit cannot cut twice as deep as a ⅛” bit. Instead, it may only be able to cut around 70% deeper.
So, if you want to cut deeper, you’ll need to use tools with larger diameters. In such cases, it’s also necessary to increase the radial depth of the cut. Ultimately, the maximum depth you can cut is limited by the diameter of the tool.
Which Material You Use (And if you use cooling)
Different materials have different levels of resistance to cutting, and so it’s generally easier to make a deep cut in wood versus cutting through metals, for example.
Also, when cutting certain materials like metals and stones, you’ll often need to use a cooling agent or lubricant to dissipate heat and prevent damage to the tool and workpiece.
However, using cooling agents limits the depth of cut because it doesn’t effectively reach deep cuts. As a result, you’ll often need to reduce the depth of cut and instead increase the number of passes or cuts made to achieve the desired depth.
Machine Limitations on the Depth of Cut
Machine limitations, such as the depth of cut, are influenced by various factors including axial depth of cut, radial depth of cut, feed rate, material, and spindle power. The relationship between these factors can be expressed using the formula:
spindle power drawn = k × axial DOC × radial DOC × feed rate
Where k is a constant that depends on the material being cut.
The axial depth of cut, radial depth of cut, feed rate, material, and spindle power depend on each other: (spindle power drawn = k×axial DOC×radial DOC× feed rate). K is a constant that depends on the material.
However, while this formula helps us understand smoe concepts, it’s often not applicable in practical situations due to the absence of the constant k for different materials.
For instance, the formula highlights that the depth to which a CNC router can cut is limited by its spindle power. To cut twice as deep (at the same feed rate and in the same material), the formula suggests that you may require 2-5 times the spindle power, depending on the extent to which you must increase the radial depth of cut.
Understanding these relationships can help with making tweaks once you consider limits with spindle power and other factors.