Key Takeaways
- CNC machine tools: These are devices or tools that enhance the performance, convenience, and safety of your CNC machine. They can help you with measuring, cutting, engraving, sanding, and more.
- Types of tools: There are different types of tools for different CNC machines and purposes. Some of the most common and useful tools are bits, end mills, face mills, ball nose end mills, V-bits, chamfer bits, drill bits, taps, grinding wheels, etc.
- How to choose tools: You should consider the quality, compatibility, material, and end workpiece of the tools. You should also check the license and profitability of the models you want to sell.
- Benefits of tools: Tools can save you time, money, and effort. They can also improve the accuracy, quality, and finish of your projects. They can also prevent damage to your CNC machine and your work area.
The right CNC machine tool is crucial for an accurate project, maximizing productivity, and extending tool life.
In fact, using the wrong CNC tool affects:
- Material Compatibility: For example, you can’t use woodworking router bits to cut metal, or you may get a poor surface finish, excessive tool wear, or even tool breakage.
- Job compatibility: A drillbit will never cut, and will break if you force it to. CNC tools have geometric limitations.
- Tool Life: Incorrect tool usage can lead to premature wear and costly replacements.
- Precision and Accuracy: Incorrect tools can result in poor dimensional accuracy and compromised part quality.
- Surface Finish: The wrong tool may cause surface defects or roughness. For example, a ball nose endmill can’t achieve a flat surface.
- Machining Efficiency: Using the wrong tool can cause slower machining speeds, longer cycle times, and reduced throughput.
- Tool Deflection: Using the wrong tool can lead to deflection, leading to potential errors, tool breakage, and increased scrap rates.
- Cost: Using the right CNC tool helps to reduce worn tools and production time, saving you money.
This article will explore the different types of CNC machining tools and their purpose. This will help you invest in the equipment that you need for your next project.
What are the main types of CNC Tools?
Different types of CNC machines use various tools:
- CNC routers and CNC mills use CNC bits, drill bits, and endmills
- CNC lathes employ turning tools
- CNC drilling tools
- CNC grinders use grinding tools.
CNC Router Bits and Endmills
CNC bits and endmills are used with CNC routers and milling machines to remove material from workpieces.
In these machines, the spindle turns the bit (just like how a drill turns a drill bit), and plunges the turning bit into the material to cutand carve.
Before we describe each bit in more detail, it’s important to first understand the difference between spiral and straight bits.
Don’t miss the article where we talk about the top must-have CNC router accessories that wil make your work in the shop much more convenient.
The Difference Between Spiral Bits and Straight Bits
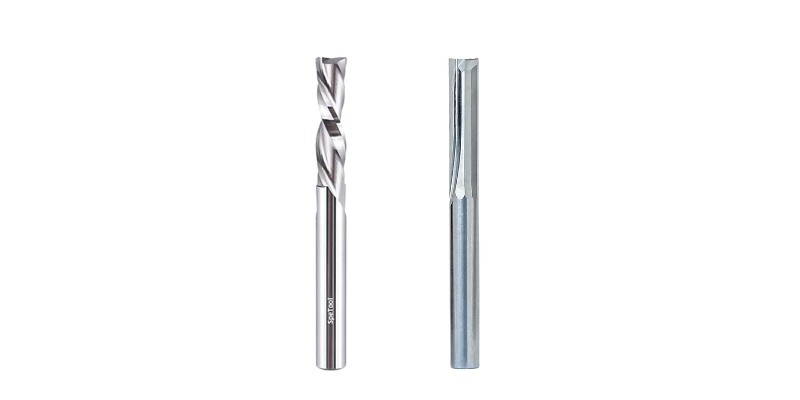
Straight bits, also known as router bits, have straight cutting edges, while spiral bits (also comprising endmills) have helical cutting edges. These differences affect how they cut material.
Straight bits cut like a chisel, producing clean edges – ideal for high-speed cutting and for woodworking. They’re typically made from high-speed steel (HSS).
However, many straight bits lack a cutting edge at the tip, which can make plunging into the material more difficult. There are, however, straight plunge router bits specifically designed for this.
Spiral bits, in contrast, can be plunged directly into the material due to their design, similar to drill bits. This, along with their versatility, makes spiral bits increasingly popular, especially among beginners.
The following cutting tools are commonly used with CNC mills:
Upcut Bits
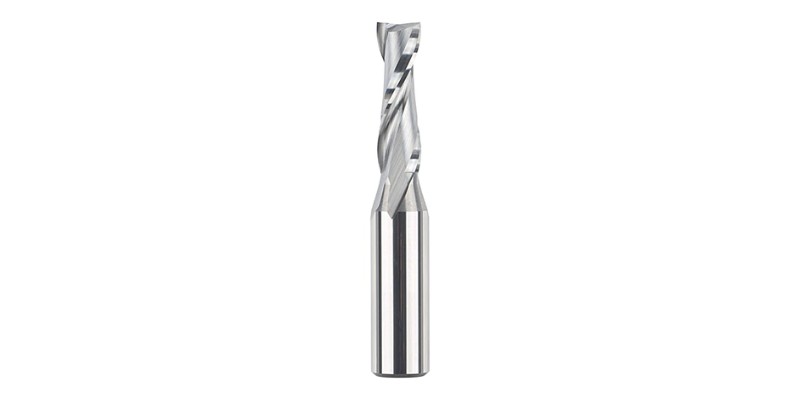
Upcut bits have a spiral cutting edge that rotates in an upward direction, extracting chips from the material when turned with the cutting tip pointed downwards.
This upward spiral action effectively pulls chips up and out of the cut. So, when you use an upcut bit and aren’t cutting all the way through the wood, it leaves a clean finish at the bottom of the cut.
The upward direction of chip removal also causes fraying, or tear-out, on the top surface.
Essentially, upcut bits create clean cuts on the bottom of the material but can leave rougher, frayed edges on the top where the bit exits the material.
Downcut Bits
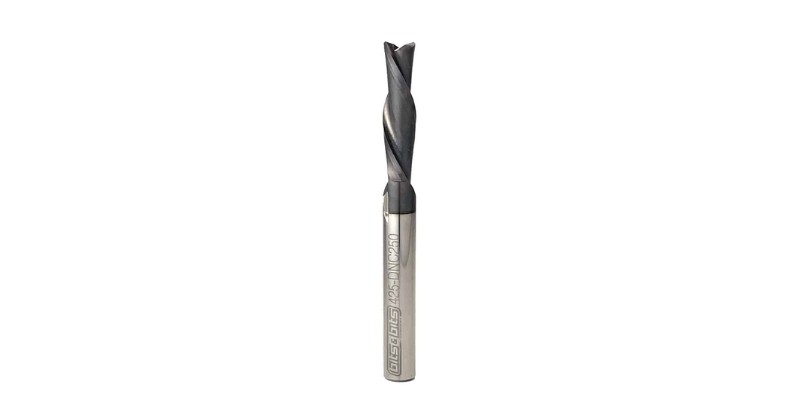
Downcut bits have a spiral cutting edge that pushes chips downwards into the material when spun with the cutting tip pointed downwards.
They essentially work opposite to upcut bits: a downcut bit pushes chips down into the cut, resulting in a clean finish on the top surface of the material, but with a rougher finish at the bottom because of the pushed-down chips.
If you’re cutting all the way through, then because there’s no bottom surface, you’ve got nothing to worry about – and you’ll just be left with a clean cut.
Compression Bits
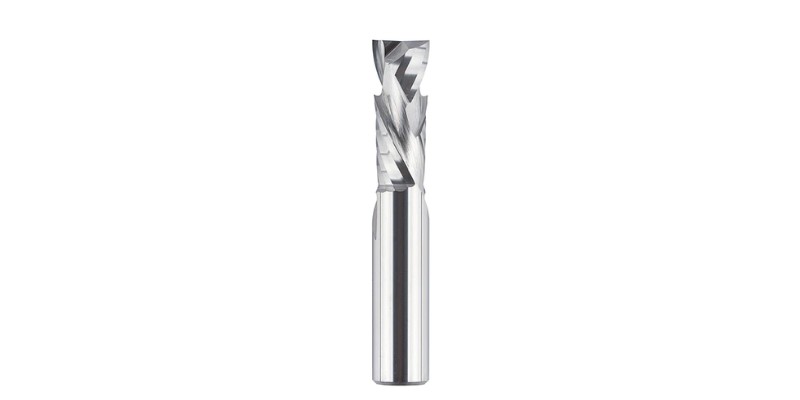
Compression bits combine the benefits of upcut and downcut bits. They feature a spiral that moves upward at the tip (like an upcut bit) and a downward-moving spiral at the larger top spirals (like a downcut bit).
As a result, the upcut part cleanly cuts the floor, while the downcut part results in a clean finish on the surface edges.
But to get the clean cut on both the top and the bottom, the bit needs to cut deep enough that both the upcut tip and downcut top are used. Basically, you need to make sure the bit is plunged deep enough into the material so the part that cuts downward also cuts.
Square End Mill
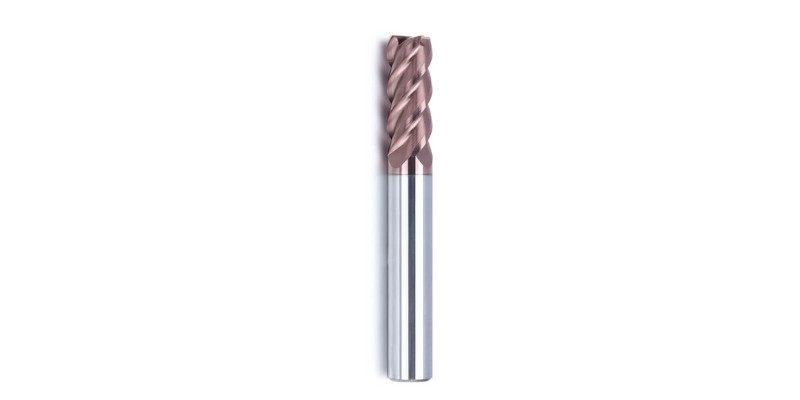
Square end mills are available in a range of sizes and are the most commonly used CNC cutting tool.
They designed to cut on both the bottom and sides of materials, making them ideal for tasks like coring cavities (hollow areas), or finishing the top and sides of a workpiece.
Ballnose End Mill
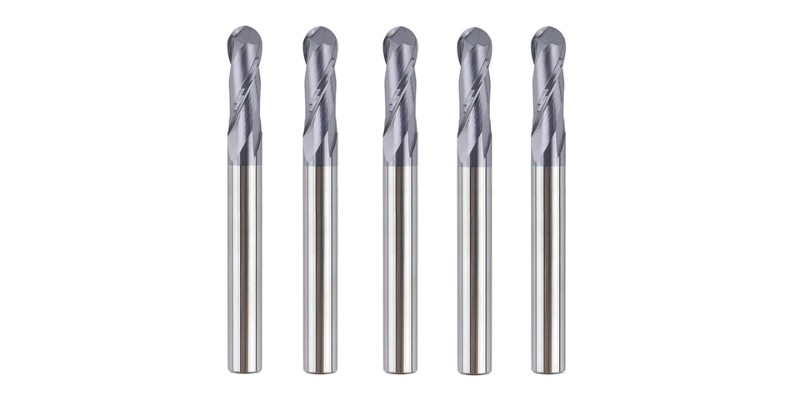
A ball nose end mill is often used in projects to achieve smooth, rounded finish, rather than sharp edges. Its fully rounded cutting end makes it ideal for 3D contouring or sculpting.
Ball nose endmills create large scallops (curved indents) when used on flat surfaces – which isn’t ideal for some uses.
However, when used on 3D surfaces, they produce smaller, more precise scallops than other tools, making them ideal for fine 3D machining and detailed sculpting work.
V-Bit (V-Cutter)
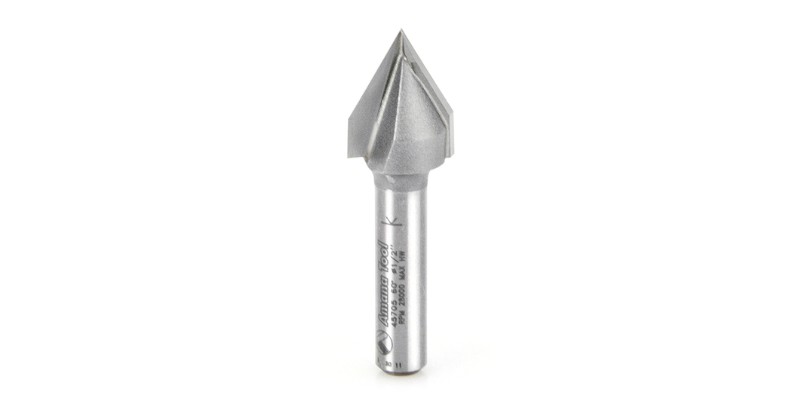
V-bits, or V-cutters, have a V-shaped cutting edge. They are specifically designed for engraving, and there’s a technique called V-carving or V-engraving dedicated to this type of bit.
The width of the cut that a V-bit makes depends on how deeply it’s plunged into the material. A shallow plunge can create very fine details, while a deeper plunge lets you cut larger areas. It’s like having a tool with a variable diameter.
Because of this, you’ll need CAM software that supports V-carving. Most free CAM software don’t offer this feature, and without it, you can’t use the V-bit (though, I’ve actually found a way to manually create a V-carving tool path with ordinary CAM software, but unless you know how to do it, you’ll need a CAM software with this feature).
One disadvantage is that V-btits are very sensitive to surface flatness. They do not produce good engravings if the surface isn’t perfectly flat.
Face Mill
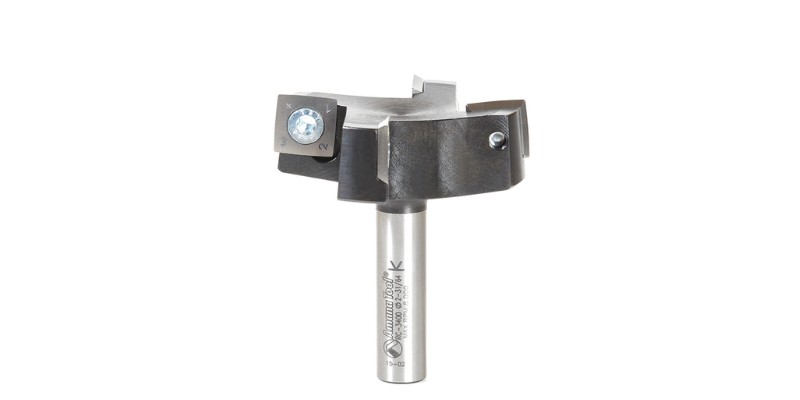
A face mill, also known as a shell mill, is typically larger than most end mills, spanning a few inches in diameter.
They’re designed for efficiently removing wide areas of material and used to create even surfaces by leveling the the stock material face. The primary purpose of face mills is to clean up a surface.
For instance, when you want to flatten a metal bar and achieve a smooth, even finish, a face mill is your best option. Face mills are designed for very shallow cutting depths, and don’t have large side cutters.
Face mills have replaceable carbide cutting edges on their sides, which makes the tool a long-lasting option. Because of this positioning, face mills are used to cut workpieces horizontally.
Chamfer Bit
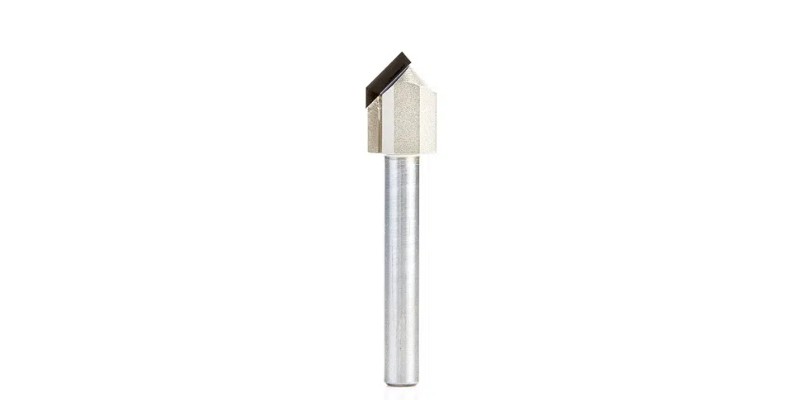
A chamfer bit, as the name suggests, is designed for creating chamfers (angled or beveled edges).
Chamfers are commonly created at 20, 45, and 60 degree angles, and are used for deburring sharp edges and corners from a workpiece to improve the part’s look and for safety.
Chamfer mills are used for creating countersinks in threaded holes. Countersinks are essentially chamfers with steeper angles, typically created at angles of 82°, 90°, or 100°. This feature allows the head of a countersunk screw to sit flush with or below the surface of the material.
Bull Nose End Mill
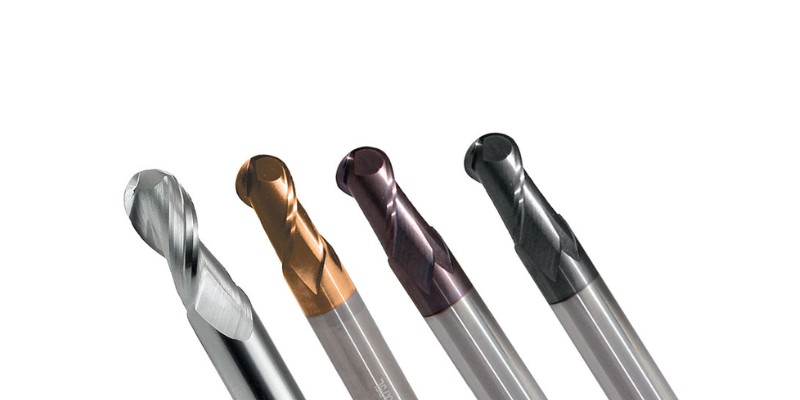
Bull nose end mills, or corner radius end mills, have rounded concave edges and are used to create smooth, “filleted” corners.
This rounded edge design leads to improved surface finishes, less chipping, and a longer tool life versus standard square end mills.
As a result, bull nose end mills are commonly used for mold-making, and other general machining to create smooth edges.
T Slot Cutter
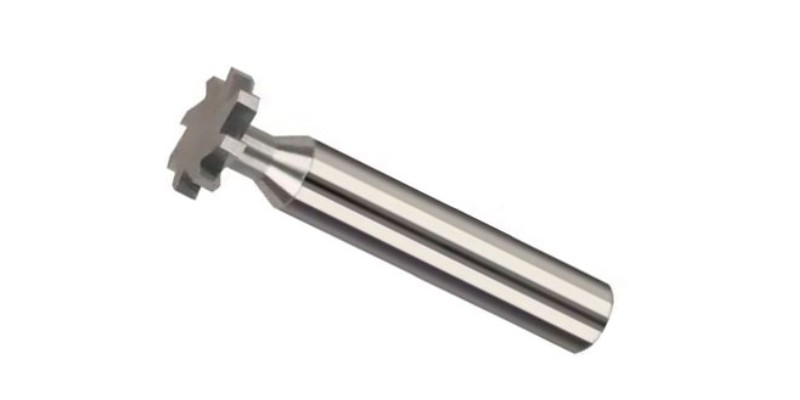
A T slot cutter it used to create T-shaped slots. T slot cutters have a thin neck connected to a large cutter.
They are used to first create a straight groove on the workpiece’s surface, before then cutting a larger and wider groove, known as an undercut, underneath the original slot – creating the T-shape. These slots securely hold bolts and other components.
Keyseat Cutters and Woodruff Cutters
Keyseat cutters, sometimes also called a “keyway cutter”, look similar to T-slot cutters and are used to cut grooves or slots in a material. Keyseat cutters can be used to cut along the side of or through a workpiece, and some designs can even create T slots. They’re available with a variety of corner geometries, such as straight edges for square undercuts, or radiused corners for rounded undercuts.
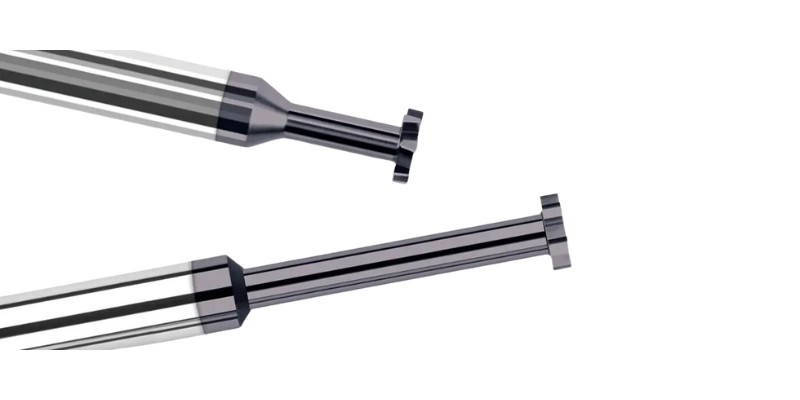
Woodruff cutters, also known as Woodruff keyseat cutters, are another type of milling cutter used for cutting specific keyways. These are typically semi-circle grooves for specialist that “Woodruff keys”. These look a lot like T-slot cutters, with a large cutting part and thin neck, but they cut different types of keyways.
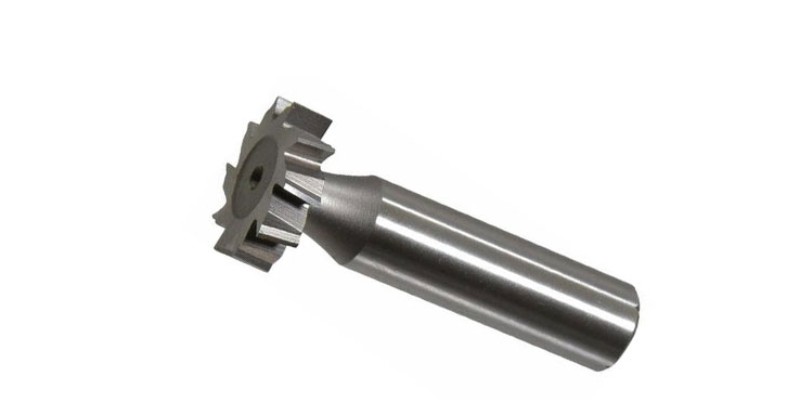
Whereas Woodruff keyways—for semicircular Woodruff keys—are mostly used for securely locking gears, pulleys, and other components onto rotating shafts, T-slots provide adjustable and secure attachment points in machine tables, so you can place and move clamps, fixtures, and various other components.
Drill Bits
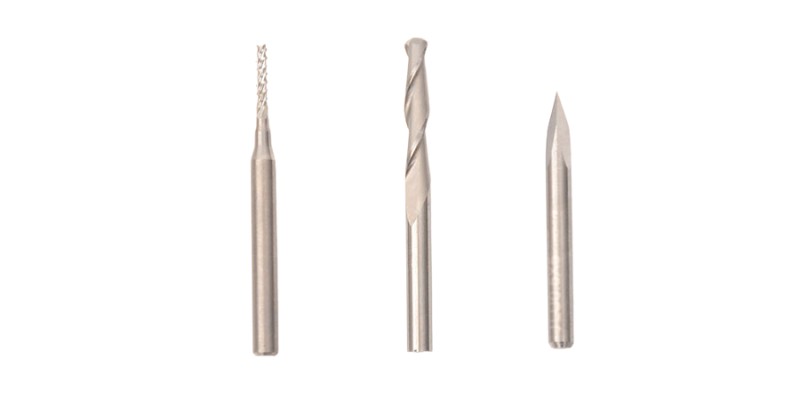
Drill bits are solely designed to be pushed vertically into the material to create a hole. They come in a range of sizes and diameters for creating specific hole sizes in wood, metal, or plastics.
They are not typically intended for lateral movement while inside the material, as this could damage the bits or your CNC machine.
However, certain specialized drill bits can tolerate some degree of lateral movement. Though, in contrast, router bits can move in any direction when inside the material, so you can make a more different cuts and shapes.
Slitting Saw
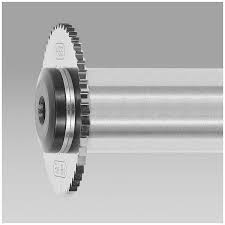
A slitting saw is a thin cutting tool similar to a keyseat cutter, commonly used in metalworking and woodworking. The tool’s wide radius and thin body allow for deeper, precise cuts and splitting parts, making it particularly suited for creating slots or grooves in a workpiece or for parting off material.
They don’t remove much material in the cutting process, so they’re often used where you need very precise control over the part’s final dimensions.
Taps
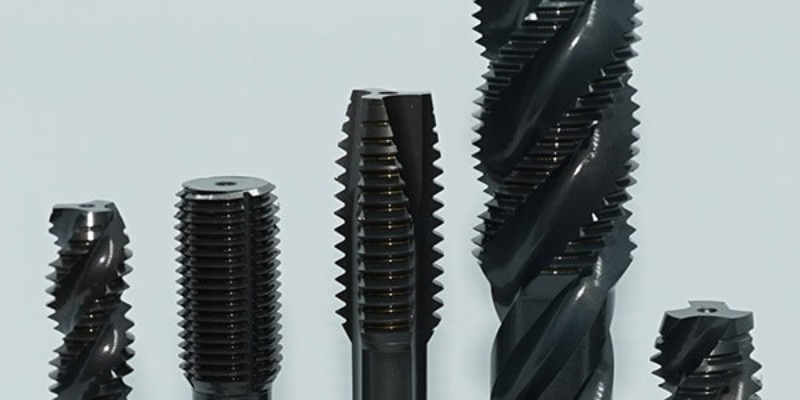
Taps are cutting tools used to create threads in holes of materials, mostly metals, for putting screws in.
Whereas wood is soft enough that some screws can directly thread them, metals are too tough, and require taps to pre-thread them. Though, you can use taps with your hands to create threads in woods and plastics, and I’ve also done this with aluminum before.
Not all CNCs are suitable for tapping however, as you need to be able to turn your spindle very slowly, at around 200RPM.
Cutting tap
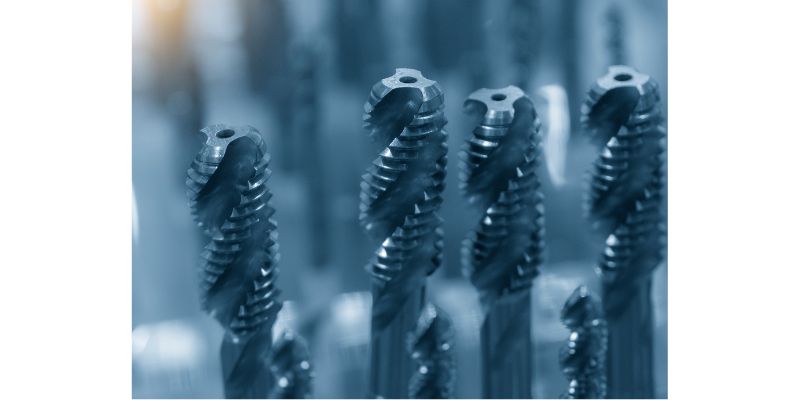
A cutting tap is a specialized tool for creating internal threads within a pre-drilled hole. You can then add a screw, and it will function like a nut would.
However, their grooves are larger and usually don’t go all the way around. Also, the ungrooved cylindrical body beneath is smaller than the matching screw. Above all, they are much harder than the material with the hole.
Cutting taps are like an enlarged screw with larger flutes (or grooves), and a narrower body. These flutes carve out material to form the threads, and also channel away the chips produced while cutting. The cylindrical body underneath the flutes is narrower than the diameter of the intended screw, so it can enter the hole the screw can’t yet fit into.
Cutting taps are often made from high-speed steel or carbide, as you need a tap made from much harder material than the material being threaded.
Forming tap
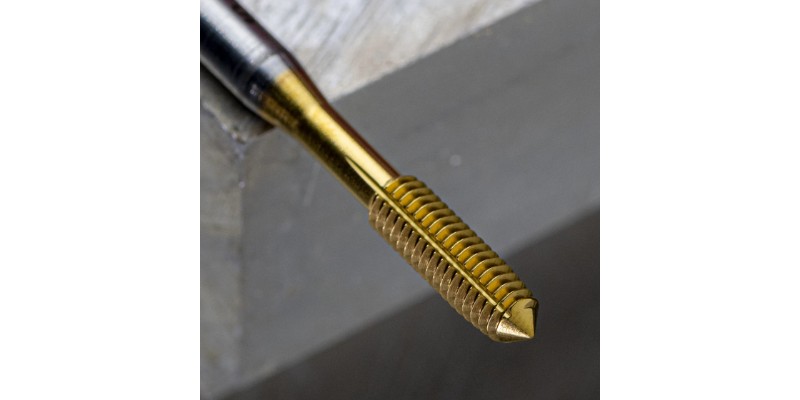
A forming tap, or roll tap, creates threads by displacing, rather than cutting, material. It uses the ductility of the material, reshaping it into threads without removing any of the material.
Forming taps are slightly conical and exploit the material’s plastic tendency to deform it into threads. It requires a slightly larger pre-tap hole compared to cutting taps since no material gets removed in the tapping process.
The tap is slightly tapered to start thread formation gradually. Because it doesn’t cut material away, the pre-drilled hole for a forming tap should be slightly larger than for a cutting tap. This process, known as thread forming or cold forming, is suitable for ductile materials but not for brittle ones.
Here are form tapping’s pros and cons over thread cutting.
Pros
Form tapping creates a stronger fastener than thread cutting. The material undergoes work-hardening when forming.
Form tapping creates no chips, so there is no need to consider chip removal, clogging, and the type of hole (blind hole or through hole).
Form tapping is done at higher speeds than thread cutting.
Cons
It’s not suitable for all materials since some materials may break instead of reshape (suitable metals include aluminum, brass, and some types of steel)
It requires more spindle horsepower.
It requires a higher speed so that forming is finished before the material goes through work hardening.
CNC Turning Tools
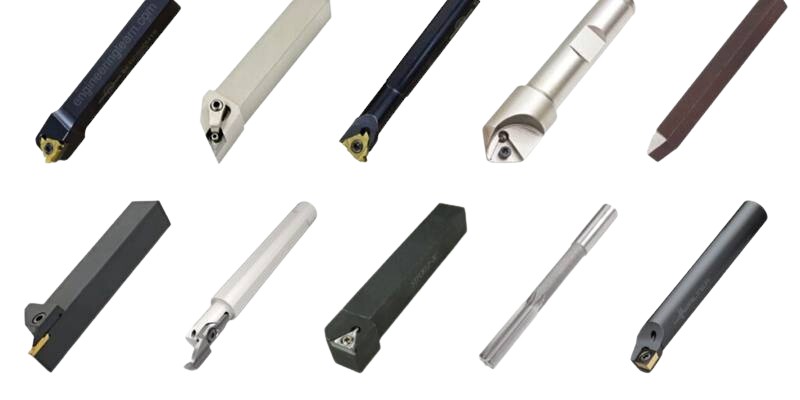
CNC turning tools are made to work with CNC turning machines (lathes). CNC lathes rotate workpieces at high RPMs to shape the workpiece.
Because turning tools revolve quickly and are used on hard materials like metals, the friction produced can result in high temperatures. So, it’s essential to use tools designed to withstand these temperatures, as well as the workpiece’s hardness.
Boring Tools
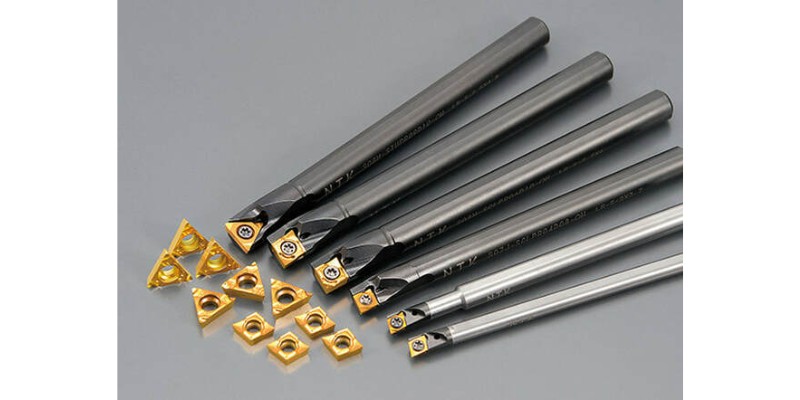
CNC boring tools are used with a turning machine to work on pre-drilled workpieces. This can help to taper, enlarge, or straighten holes for different purposes, often in the aerospance, automotive and toolmaking sectors.
Using a boring tool to enlarge a smaller hole is much more accurate than using a larger drill, as boring is slower and more precise, so it’s ideal for creating accurate and smooth finishes within holes.
Chamfering Tools
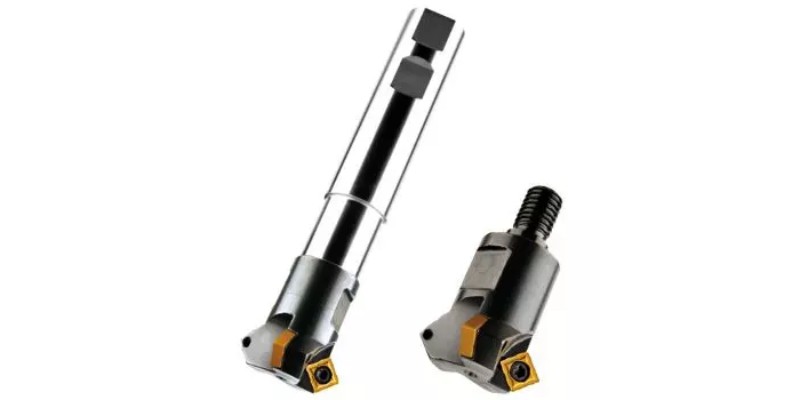
Chamfering tools are used with turning machines (as well as CNC mills) to remove sharp edges and produce a beveled or angled edges, and for deburring.
Chamfering also helps provide a guide for bolts or screws, as well aiding in wear-and-tear resistance, and in creating grooves for the weld material to prepare metal parts for welding.
Parting Tool
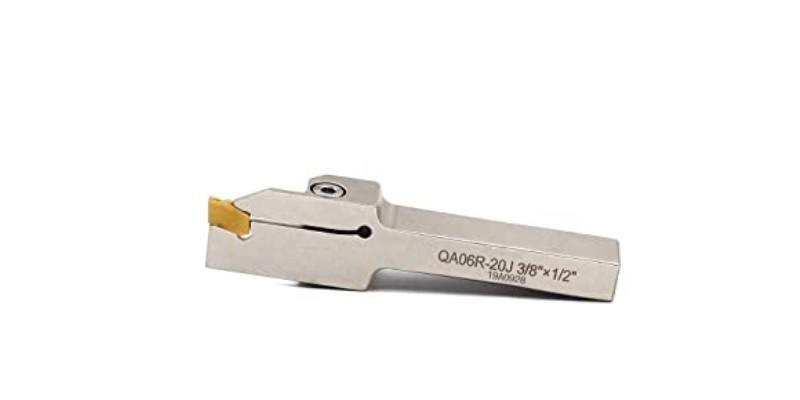
Parting tools, also known as cut-off tools, have a sharp edge like a blade, and are used to cut or remove sections of a workpiece on a lathe. Though, parting tools are also sometimes used for grooving rather than full cutting.
While the spindle is spinning the material, the parting tool is slowly inserted into it, like a knife cutting into a potato until a portion is separated.
Knurling Tool
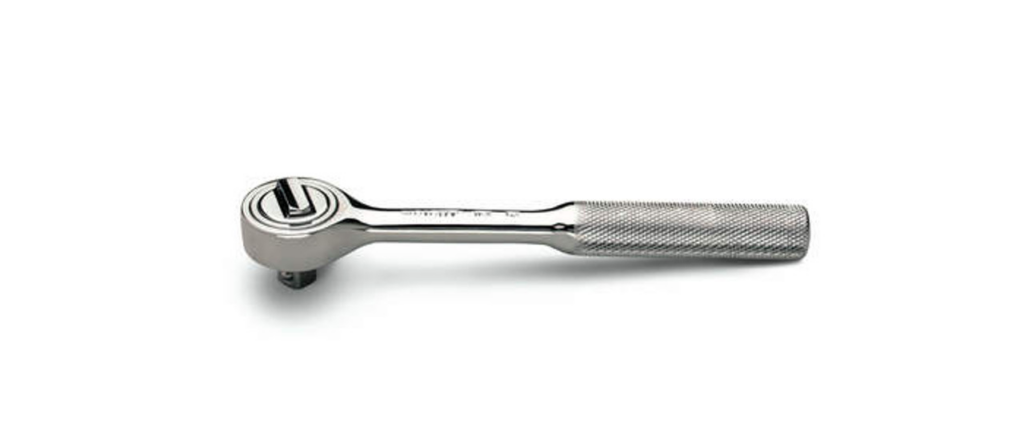
A knurling tool is used to produce patterns on the workpiece, including diamond knurls, straight lines, and diagonal lines.
Kurling tools have a set of hardened steel rollers, etched with the pattern you want to press into the workpiece to create the pattern.
Some knurl a surface for its aesthetics, but knurling is primarily done to improve grip when you hold it in your hands. For example, many drive ratchets and other tools, and other knobs and components have knurled surfaces for better grip.
CNC Drilling Tools
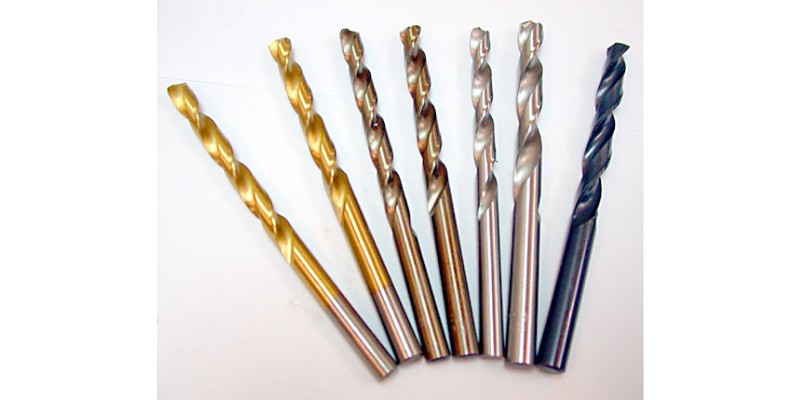
CNC drilling tools and drill bits are used by machinists to create accurate holes in workpieces. CNC mills and twist drills are used alongside a range of drilling tools.
The following CNC drilling tools are commonly used by machinists:
Center Drills
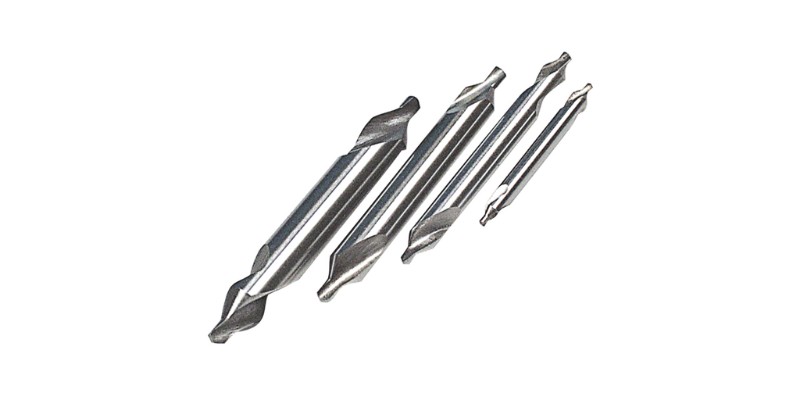
Center drill bits (also known as centering drills, combined drills, or countersinks) are used to create an initial, precise pilot hole at the start of a CNC drilling machine operation. This initial hole acts as a guide and can be altered by using other CNC tools to enlarge or alter it for a specified purpose.
Their main purpose is to create a guide so that the final hole created by other tools is accurately positioned and perfectly aligned. This small hole helps prevents the larger drill bit from deflecting or wandering.
Twist Drills
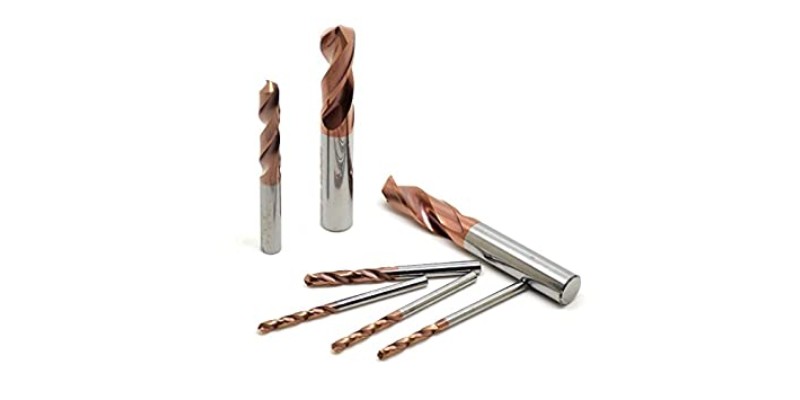
Twist drills are the most common type of drill bit, and use two spiral flutes and a pointed tip. If you’ve ever drilled a hole in wood, plastic, or metal, you’ve most likely used a twist drill bit.
However, twist drills are not ideal, in most cases, for drilling masonry, walls, ceramics, and concrete – standard twist drills will wear out quickly or perhaps even break. They’re best for drilling metals and softer materials.
Ejector Drills
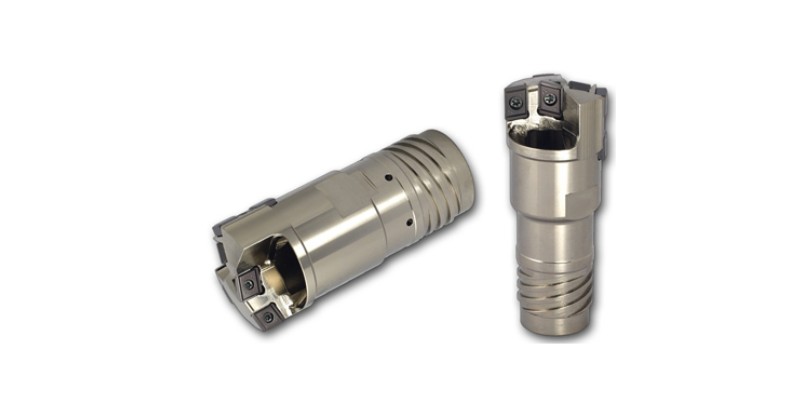
Ejector drills are used for drilling deep holes, particularly in metals. They can create holes that are several feet long, and used with machining centers – specialized machines used for very precise deep drilling.
Being able to drill such deep holes makes ejector drill bits ideal for the oil and gas industries, aerospace, and more.
CNC Grinding Tools
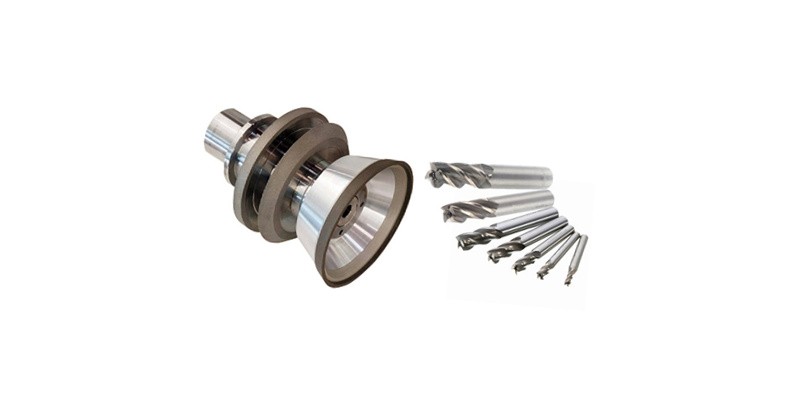
CNC grinding tools are used with grinding wheels to create a smooth surface on a workpiece. CNC Grinders are the most effective method for removing material removal from large surfaces and cylindrical objects.
Therefore, grinding tools are mostly used for finishing a surface, or cutting a material down to a smaller size before processing it with another machine.
Surface Grinders
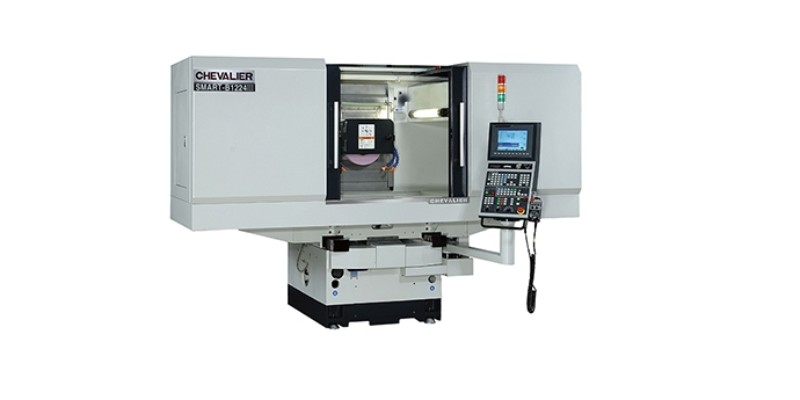
Surface grinders are the most common type of grinder used to produce a polished finish on flat metal surfaces. They’re widely used in toolmaking, general metalworking, and various areas of manufacturing for precision grinding, generally flattening surfaces, removing stock material and producing very precise parts.
Surface grinders use a reciporacating or rotating table, an abrasive wheel, and a chuck that holds the workpiece in place. The table moves back and forth or rotates, so you have precise control over the grinding process.
Then, the abrasive wheel, usually made from diamond, removes material from the workpiece to create your desired finish on the surface.
Cylindrical Grinders
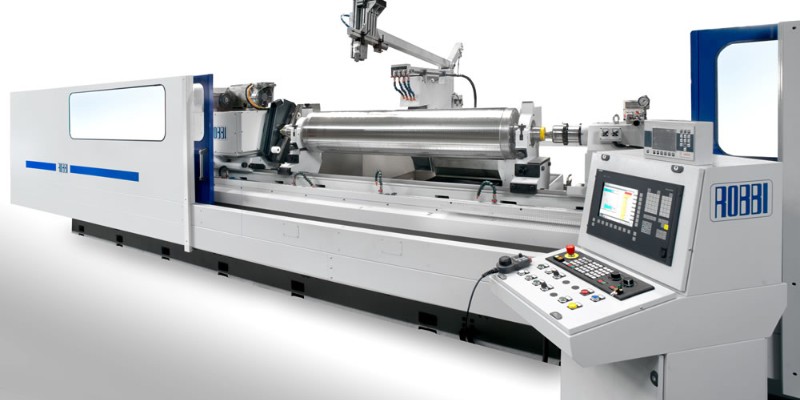
While surface grinders are best suited to flat workpieces, cylindrical grinders are specifically designed for working on round or cylindrical workpieces.
This makes cylindrical grinders better for working on:
- Cylinders
- Rods
- Shafts
- Crankshafts
- Tubes
Cylindrical grinders typically have a rotating wheel or grinding head that moves along the length of the cylindrical workpiece, so you can remove the material and achieve your desired shape and finish.
They’re used widely to produce compoennts for the automotive, aerospace, and precision engineering industries.
Precision ID & OD Grinders
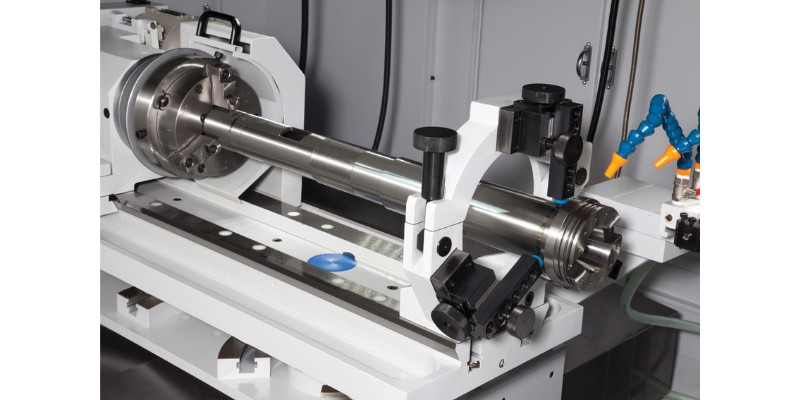
The ID and OD in these CNC grinding tools stands for outside diameter, and inside diameter. These form one tool that can do both tasks, whereas you would need separate cylindrical grinders for this.
While it is possible to use cylindrical grinders for OD projects, a cylindrical grinder will lack the level of precision and surface finish that dedicated ID and OD grinders offer on cylinder parts.
They’re typically used in the aerospace, automotive, and medical industries where high precision is crucial. Typical applications include grinding bearing races, bushings, shafts, spindles, gears, and other precision mechanical parts that require accurate dimensions and smooth surfaces to work properly.
Centerless Grinders
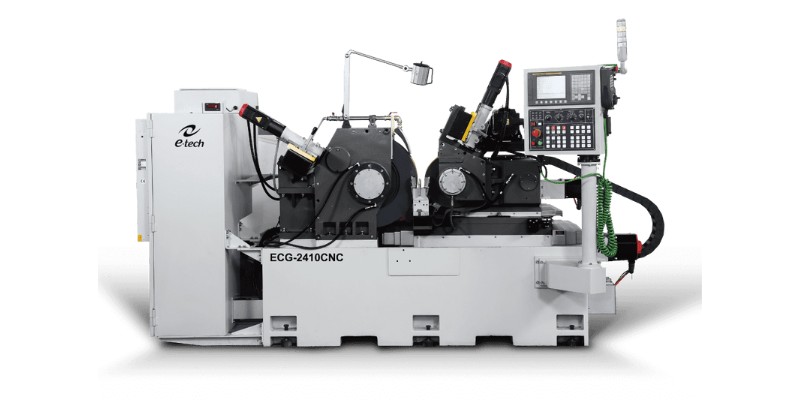
Centerless grinders do not use chucks or centers to hold the workpiece in place. Instead, the workpiece is fed between a small regulating wheel and the grinding wheel while resting on angled supports.
The grinding wheel forces the workpiece into the smaller wheel and supports it to keep it steady. The regulating controls speed and feed rate as the grinding wheel removes parts of the material. The angled supports, called workrest blades or work guides, keep the workpiece stable as material is removed.
Centerless grinding is an excellent method for creating accurate, round surfaces. As a result, it’s often used for creating high-precision shafts, pins, and other components.
What Materials Are Used to Make CNC Machine Tools?
High-performance materials that can withstand pressure and high temperatures used to make CNC machining tools include carbon steel, tungsten carbide, high-speed steel, cemented carbides, and cutting ceramics.
As a rule of thumb, materials used in cutting tools need to be twice the hardness, on the hardness scale, of the material being cut.
The following types of CNC machine tool materials are often used:
Carbon Steel
Carbon steel is commonly found in CNC machine tools that are used for low-speed operations. These include:
- Forming Tools
- Twist Drills
- CNC Cutting Tools
- Turning
Carbon steel has a higher carbon concentration than other steel types. This can be anywhere between 0.05% to 2.5%. Most other steel types typically have a maximum carbon content of 0.3%.
Carbon steel is regularly used in CNC tools because of its high tensile strength, and it’s also relatively inexpensive in comparison to other materials.
High-Speed Steel
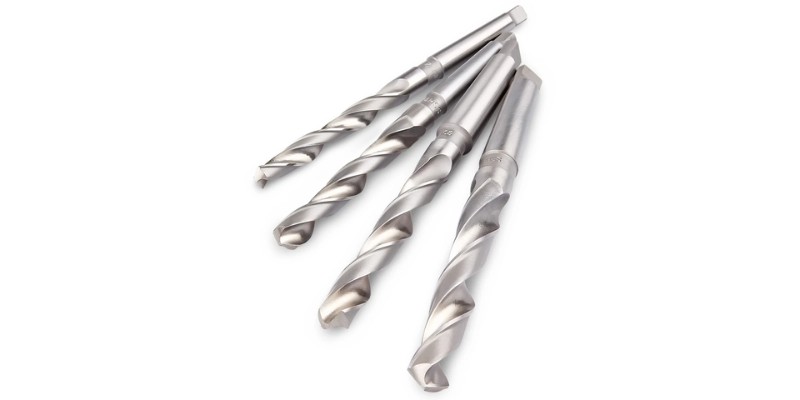
High-speed steel (HSS) is an alloy that is made from tungsten, molybdenum, and chromium. It’s known for its great strength and wear resistance compared to materials like carbon steel.
High-speed steel is used in the manufacturing of high-speed CNC machine tools. This is because of its ability to retain its strength at high temperatures. High-speed CNC machines create a great amount of friction that can heat materials quickly, and so using a material that can withstand this is essential.
This makes it an excellent material for CNC cutting tools and drilling. One drawback however is its high cost, though HSS tools typically last for a long time, and so can offer good value over the long-term.
Cemented Carbides
Cemented Carbides are typically used for CNC cutting tools. For cemented carbides, cobalt is used as a metal binder with tungsten carbide for the hard carbide phase.
This material is known for its great wear resistance and strength. It’s also heat resistant, and is resistant to corrosion and oxidation, making it perfect for CNC cutting tools that need to withstand high temperatures.
Cutting Ceramics
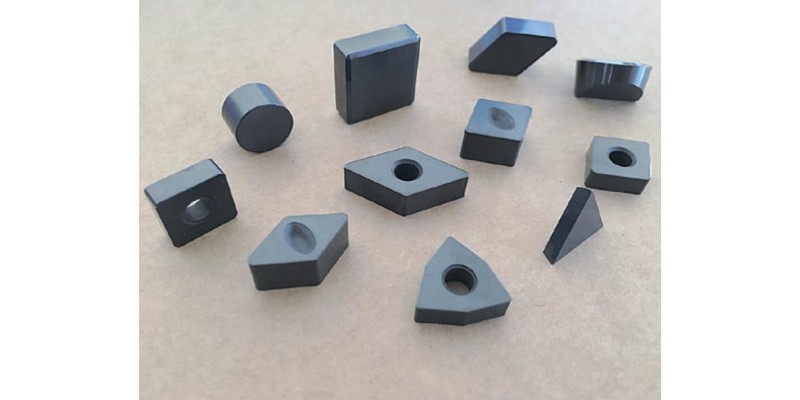
The use of ceramics in CNC machining is relatively commonplace, because they’re so wear- and heat-resistant. Ceramics are made from silicon nitride and aluminum oxide and are corrosion-resistant.
Ceramic CNC tools are an effective cutting tool for hard steels, superalloys, and cast iron.
Tungsten Carbide
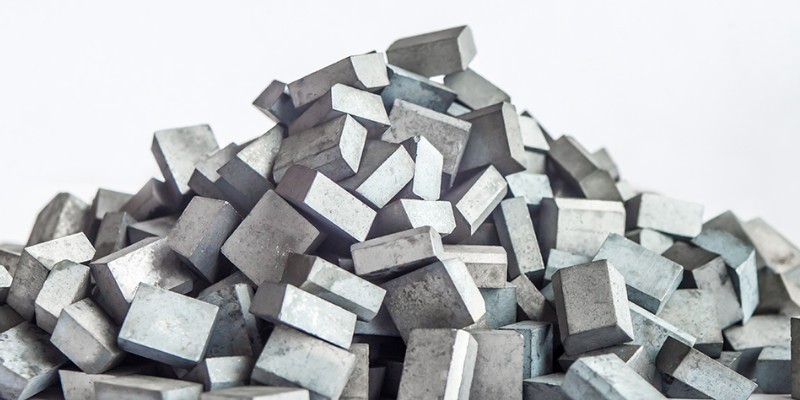
Tungsten carbide is an incredibly strong chemical compound, made up of equal parts carbon atoms and tungsten. It’s used to create milling, drilling, turning and threading tools designed to cut tough materials.
Tungsten carbide tools also provide great resistance to extreme temperatures and force. This minimizes the risk of breakages or poor performance.
These desirable qualities ensure the cutting tools made from it last a long time, and make it effective for machining hard metals like stainless steel, cast iron, and titanium.
Final Thoughts
When choosing tools for CNC machines it is essential you select the right type, quality, and standard to meet the requirements of your specific job.
The right tool will also be determined by the workpiece material and project you are carrying out.
This is true whether you are creating internal or external threads on existing holes, or require the right CNC machining tools to cut flat surfaces.
Hard-wearing, strong, and temperature-resistant materials are essential for creating these cutting tools for CNC machines. Ceramics, carbon steel, high-speed steel, and tungsten carbide all offer excellent qualities.
Though, hard-wearing tools for CNC machines typically have a higher price tag – but they make this up over time as they are longer-lasting.